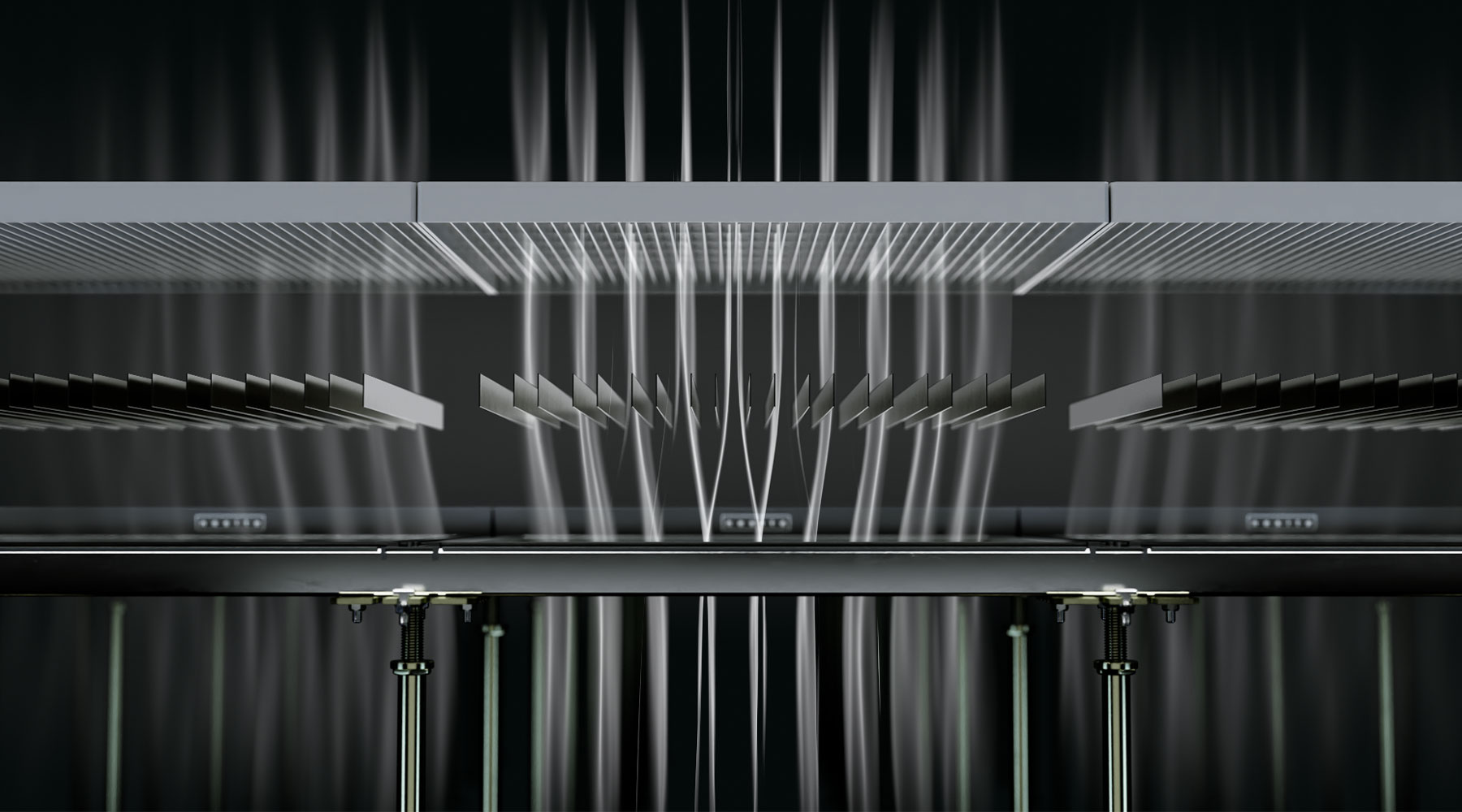
Home / News / Eventi /
For managing and controlling airflow in data centres, using raised floors is a common and established practice. Despite the widespread and design for this function, their efficiency is often the subject of comparison. In this article, we will explore the characteristics and performance of raised floors in this context, seeking to provide a clear and comprehensive overview.
Airflow and raised floor sealing
Management and control of air flows are essential for the optimal operation of machines in a data centre; inefficiencies in this regard can compromise operations due to inappropriate temperature regulation, increasing maintenance costs and energy consumption. For this reason, the integrity and correct installation of the raised floor are some of the most important aspects in an optimal underfloor air distribution system.
Possible causes of underfloor air leakage
Starting from the premise that the raised floor is designed to ensure efficient air distribution in the plenum, some conditions can interfere. The main factors that ensure the airtightness of the subfloor, and should therefore be carefully considered, are:
- DIMENSIONAL ACCURACY
Ensure that the floor system is Class 1 according to EN 12825, which regulates panel dimensional tolerances.
- PANELS EDGE TRIM
The panel must be provided with edge trim, which is essential for sealing the gap between the floor panels. Its absence can in fact cause significant air leakage.
Columns and stringers, which form the support structure for the panels, must be equipped with gaskets. The perimeter of the room is often a major source of depressurisation. It is essential to ensure that the system provides for the use of an appropriate gasket to guarantee airtightness on the room perimeters.
- INSTALLATION AND MAINTENANCE
Correct installation is a prerequisite for the airtightness of the subfloor, and should therefore be carried out by professionals. During maintenance, on the other hand, care must be taken not to damage or displace the gaskets of the stringers and pedestals; if damaged, replace them.
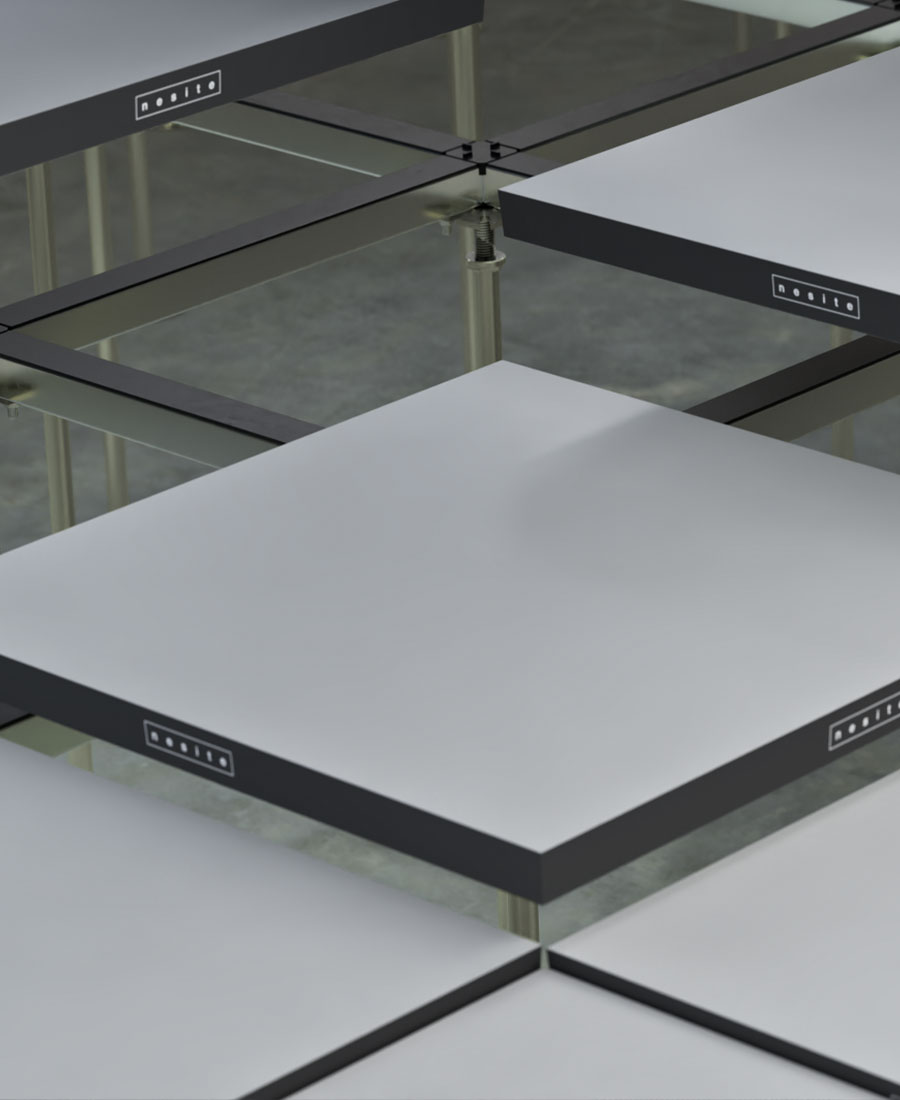
AIR LEAKAGE TEST, THE PERFORMANCE
In order to quantify the level of a raised floor’s air leakage under optimal conditions, a laboratory test was carried out using a standard configuration of modules and their substructure.
Specifically, the mockup – consisting of 4 panels 600x600mm and 500mm high – was placed in an airtight chamber and sealed around the perimeter. A fan was fitted to the airtight chamber by a duct to supply airflow into it at different air pressures. The controller allowed to vary the airflow rate and maintain a constant rate for a while sufficient to obtain readings of airflow rate and pressure.
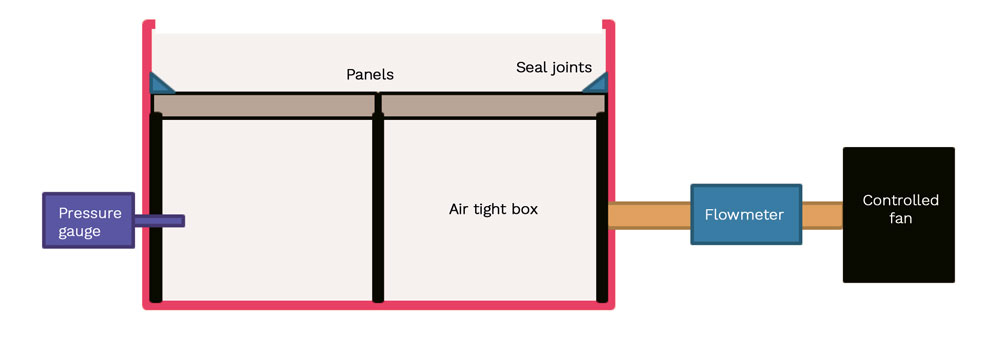
Four tests with a different assembly of the panels were performed:
– test with zero gap between panels: aluminum adhesive was used to close all panel gaps;
– test in standard installation mode: panels were positioned normally, as it happens on site;
– test with a 0.3mm panel gap;
– test with a 0.6mm panel gap.
NOTES
The purpose of the last two test configurations was to simulate the use and condition of the access floor over time.
For each test the air leakage rate was measured and calculated as litre per second per meter length of joint in the range of pressure 0 – 120 Pa (limit of performance of the apparatus).
The test included a preliminary smoke test to verify the good installation of the access floor between the panels and along the perimeters of the walls. Pressurised smoke was then diffused into the plenum to make any air leaks due to faulty construction or incorrect pipe connections immediately visible.
TEST RESULTS
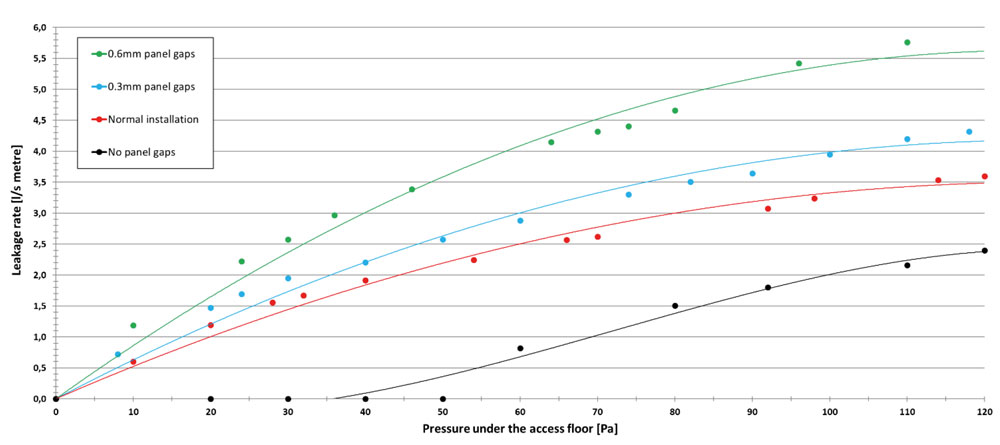
The test confirms that the raised floor designed and installed properly ensures optimal plenum pressurisation, avoiding leaks and consequent inefficiencies.
For reference, the pressure under the floor at which the panels theoretically begin to rise is equal to the weight of the panel per unit area. For example, for the PG6ALV panel (calcium sulphate core, steel bottom covering, vinyl finishing) is approximately 500 Pa.
Data centre cooling systems, forecasts and conclusions
Data Centres are currently a rapidly expanding sector, driven by the integration of artificial intelligence. Indeed, next-generation data centres will have to offer ever-increasing computing, processing and data storage capacities, while implementing efficiency and sustainability.
In this regard, we would like to point out an interesting article by Cosimo Verteramo, Life Science & High Tech Division Director of Deerns Group, which comprehensively explains this trend.
Given the large amount of data to be processed, with the consequent increase in energy consumption, it becomes essential to take action to improve the efficiency of cooling systems.
Nesite, with more than 60 years of experience in the sector, guarantees optimal pressurisation of its underfloor ventilation systems, which can be supplemented by joints sealing (Labfloor system). In addition, the company’s commitment to sustainability is confirmed by the most authoritative international certifications, such as FSC, EPD, CE Marking, Cradle to Cradle.